Concrete board, better known as the cement board, is a useful and common building material that can be found in a variety of places. It can be found throughout many homes, in bathrooms, kitchens, and dining rooms.
Concrete board is a mix of plant fiber and a cement binder. It is primarily used as backing for tile due to its structural strength, its long life, and its strong resistance to water damage. It can be used in both the interior and exterior of the home and serves a similar purpose to drywall.
A lot of projects end up using cement board for a lot of reasons. It works great for showers, countertops, and even for some floors. But why is it useful for these things?
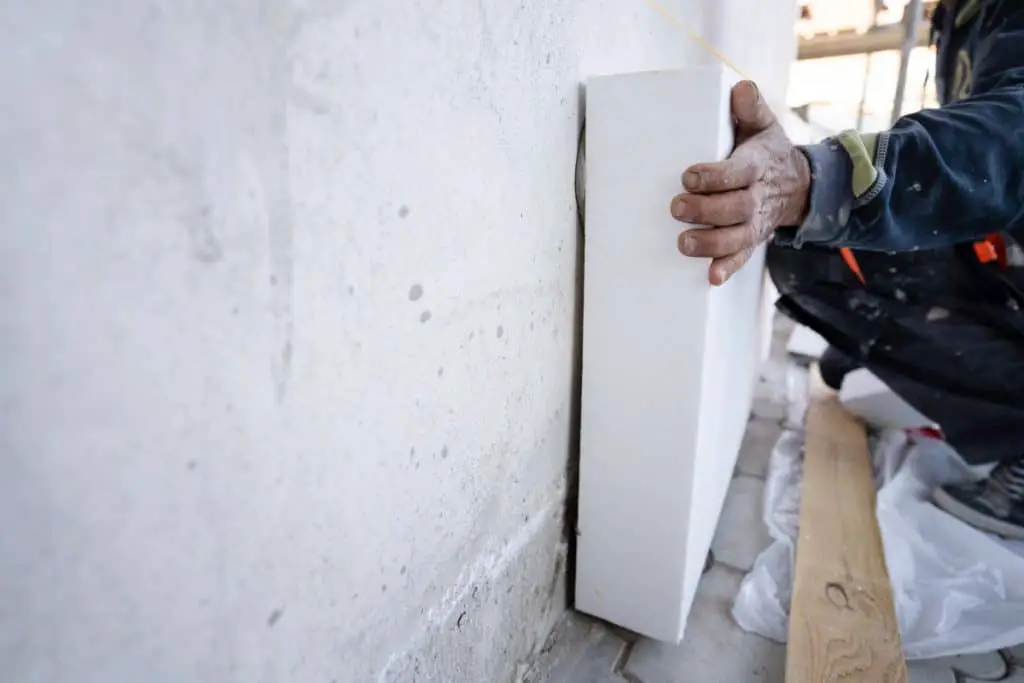
Table of Contents
What Is Cement Board Made Of?
Cement board is a simple mixture of either cement and particle board or cement and various plant fibers. The cement in the mixture acts as a binder, holding all the plant matter together.
The particleboard or the fiber act as reinforcement for the structure, providing the cement board with its signature strength.
The two different kinds of cement boards are mostly interchangeable, although they do have a few different properties that make the fiberboards more desirable for household projects.
While wood fiberboards are a bit more expensive, they tend to be more water-resistant and a little lighter than their counterparts.
How Is Cement Board Made?
Like drywall, cement board is what’s known as a prefabricated building material.
That means that rather than produce the material on-site, workers make it in a factory, and then it is moved from the factory floor to the place it is needed (potentially with the help of a middleman like a hardware store.)
This saves time when it comes to some of the longest parts of the construction process, namely the drying period for cement. Because the cement is dried even before it is shipped, the time it takes to install is drastically reduced.
There are actually a few different processes by which the cement board can be made. According to Global Cement, there are three primary procedures used by different companies, but the most common one is known as the Hatschek Process. Source
“…unbleached cellulose fibres are re-pulped in water and then refined before being mixed with cement, silica and various additives. The mixture is deposited onto a wire substrate, vacuum de-watered and cured to form a cement board sheet.” Source
Sheets made this way are often used for roofing products, as they tend to be able to weather all sorts of harsh environments. They’re also used for showers, bathrooms, and countertops for the same reasons
Similarity To Drywall
As mentioned earlier, cement boards are similar in their production cycle to the drywall. Both materials can be used to back walls, and both are prefabricated off of the construction site.
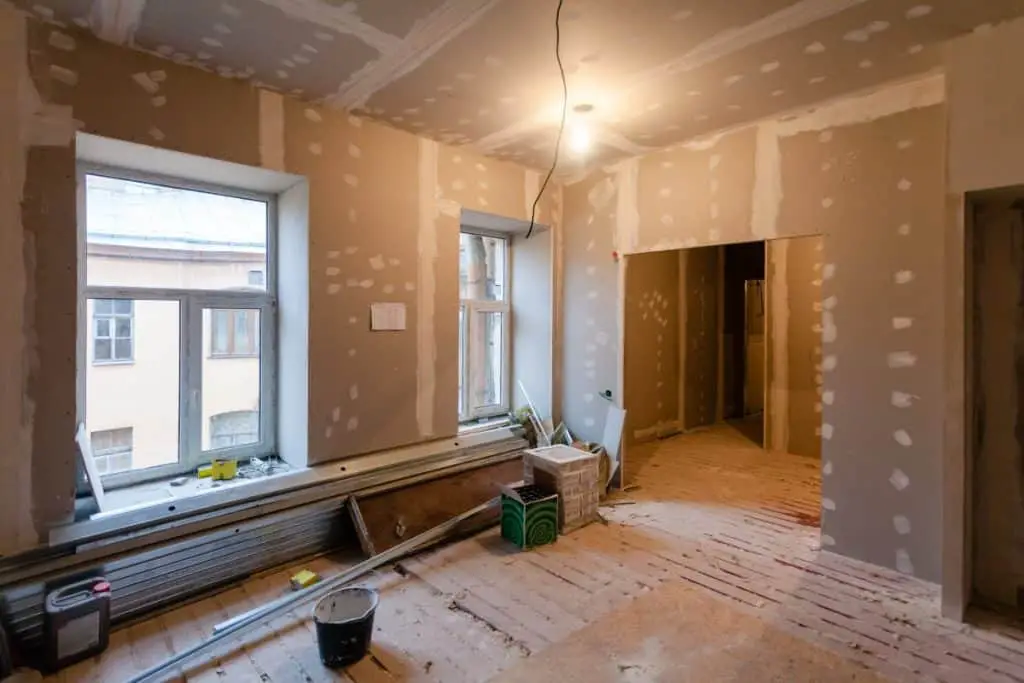
The main differences between drywall and cement board come down to price, weight, and properties.
Cement board can be an expensive up-front investment due to its weight and the sheer amount of effort that it takes to install. This makes it undesirable as an alternative to drywall in a lot of situations. While drywall isn’t exactly cheap either, it’s certainly a lot cheaper than the cement board.
Its weight also makes it difficult to install without professional help. It generally takes two people to move one sheet of cement board, even if it isn’t very big. This is a contrast to drywall, which is often light enough to install with just one or two people.
However, the specific strengthening properties of the cement board make it a fantastic option to back tile, and its water-resistance makes it useful for a lot of outdoor projects.
The cement that is prominent in the mixture also makes it resistant to fire and most kinds of vermin. It’s also much more impact resistant than drywall, which can, rather infamously, be punched through fairly easily. These factors all add to the cement board’s already significant resilience factor.
What Makes Cement Board Ideal For Supporting Tile?
When it comes to water protection, tile and grout actually don’t do a very good job. This means that where the tile is supported only by wood, mold, mildew, and decay are all inevitable.
This can cause serious structural problems in a tile wall or floor, especially in a bathroom or shower. Cement board, on the other hand, resists all kinds of water damage extremely well. While the cement board isn’t technically waterproof, it dries easily and it absorbs water in a way that doesn’t endanger its structure.
This goes for floors as well as walls since wood floors can easily sustain water damage over a long period of time. Cement board can be applied as a subfloor underneath the tile and above wood to protect the wooden floor.
On more water-resistant surfaces like concrete or stone, it isn’t usually necessary to use the cement board as a subfloor. In these situations, tile can be applied directly over the already existing flooring.
Other Applications
Veneer Stone: Veneer stone can’t be applied to wood, as wood will suck moisture out of the mortar. It also can’t be applied to drywall, which isn’t strong enough to support its weight. It can, however, be safely applied to cement board
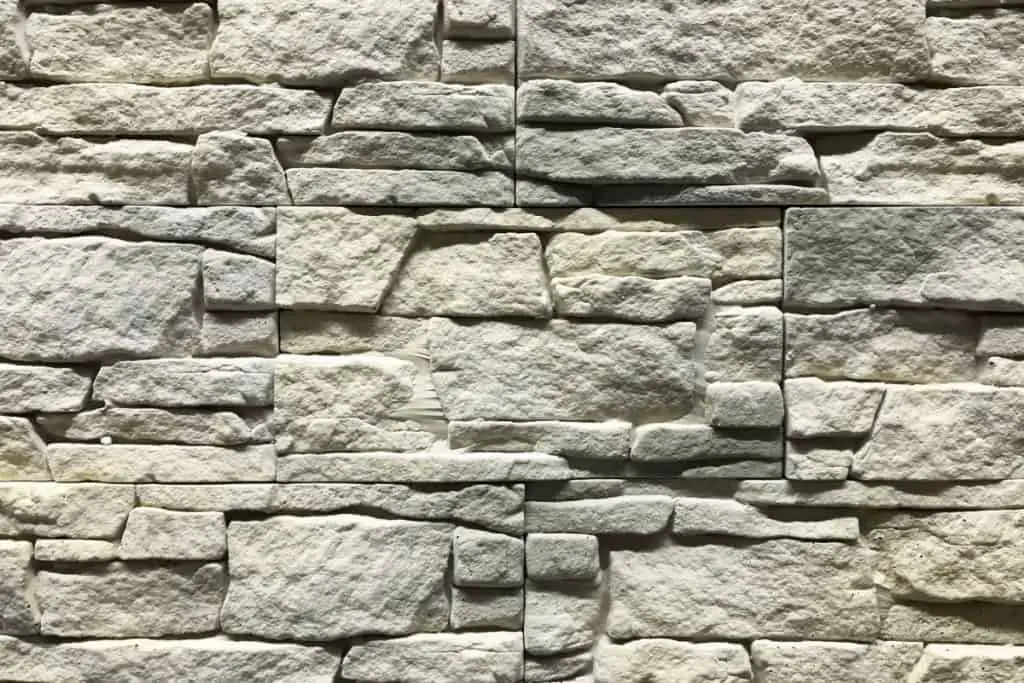
Roofing: Specialized cement board can be used for roofing and insulation. Because it resists water so well and can hold a lot of weight, it can be a long-lasting option for sub-roofing.
Countertops: A concrete board can be used in place of a mortar bed in many countertops. It’s fairly easy to install on a plywood frame, and like with the other applications its strength and water resistance make it a long-lasting option.
Acoustics: Cement board is at least partially made of wood, which makes it pretty good for absorbing sound and improving the acoustics of a small room.