Concrete, tarmac, and asphalt are three materials you likely see every day. Visually, it is not difficult to tell the difference between the three, but other than that, what is different about them?
The difference between concrete, tarmac, and asphalt is the materials they are made with. Concrete is made of aggregate and cement. Tarmac is made with crushed stone mixed with tar. Asphalt is made from stone and bitumen. Other differences include uses, durability, and price, to name a few.
These differences are interesting, but what do they mean? In this article, we explain the uses, qualities, and differences of concrete, tarmac, and asphalt.
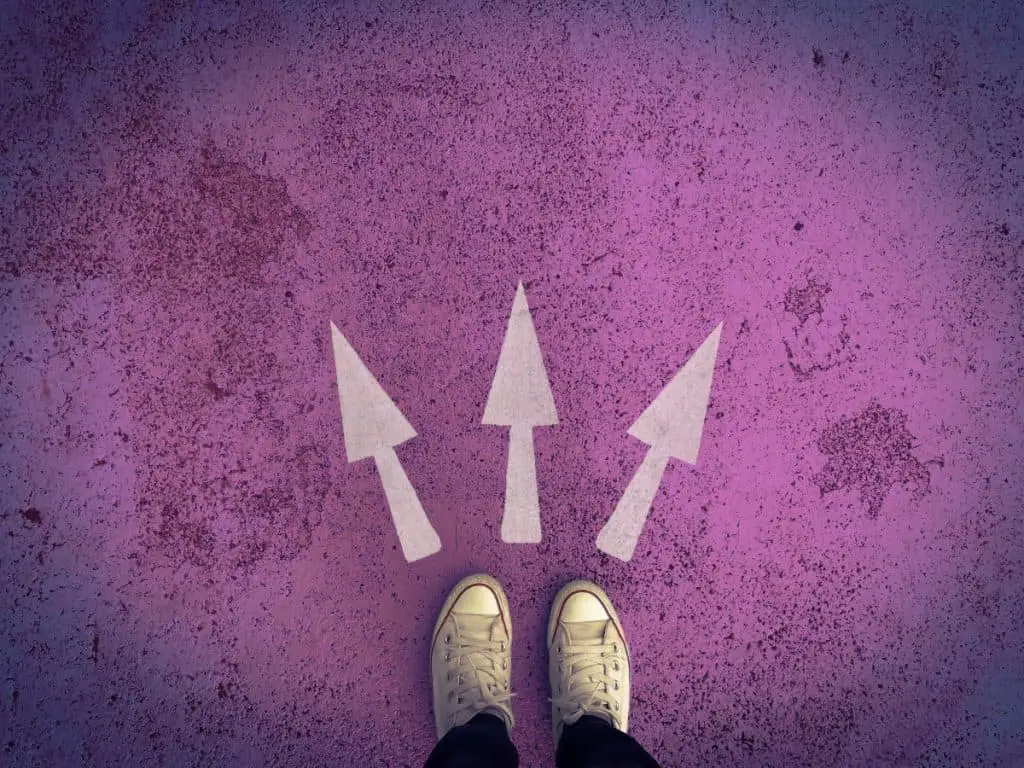
Table of Contents
Concrete
When attempting to discover the differences between comparable things -such as finding the difference between concrete, tarmac, and asphalt- it is useful to investigate each thing separately to see what makes it unique from the others.
This is exactly what we’re doing in this article. The first of the three materials that we’ll be dissecting is concrete.
Concrete Components
Basic concrete has three ingredients or components that make it up:
- Portland Cement
- Water
- Aggregates
Portland cement is cement that is made up of ground down limestone and clay. This cement is mixed with aggregates and water to make a hardening paste. When this paste hardens, it binds the cement and aggregates together, creating stable concrete.
The second material that makes up concrete is water. As explained previously, water serves as an agent that interacts with the cement to make it both a workable and easily hardened material.
When mixing concrete, the water/cement ratio is something to pay close attention to. Mixes with more water will be weaker and thinner, whereas mixes with less water will be stronger and much denser.
Read more: What Happens When Concrete Is Too Wet?
The last basic component that makes up concrete is the aggregates. This is a word you may not have heard before, but it refers to common things like sand, rocks, and gravel.
Aggregate materials are small inert (chemically inactive) materials that add grain, texture, and strength to the concrete. All concrete mixes typically contain fine and coarse aggregates. Sand is usually the “fine” aggregate, and gravel or crushed stone is usually used as the “coarse” aggregate.
Installation And Uses
Now that we know the basic components of concrete, let’s take a look at its installation and uses.
Unlike other hard building materials such as brick or stone, concrete is installed as a wet, pourable, and malleable material. It is mixed either on-site or before installation at a concrete batch plant and transported to the installation location with a concrete mixer truck.
When the concrete is mixed and ready, it is poured into excavated spaces that are supported by removable wooden frames, usually called concrete forms. Depending on the structure, internal strengtheners like rebar or wire are put into the concrete to strengthen it from the inside out.
Recommended reading: When Do You Need to Add Rebar to Concrete for Extra Strength?
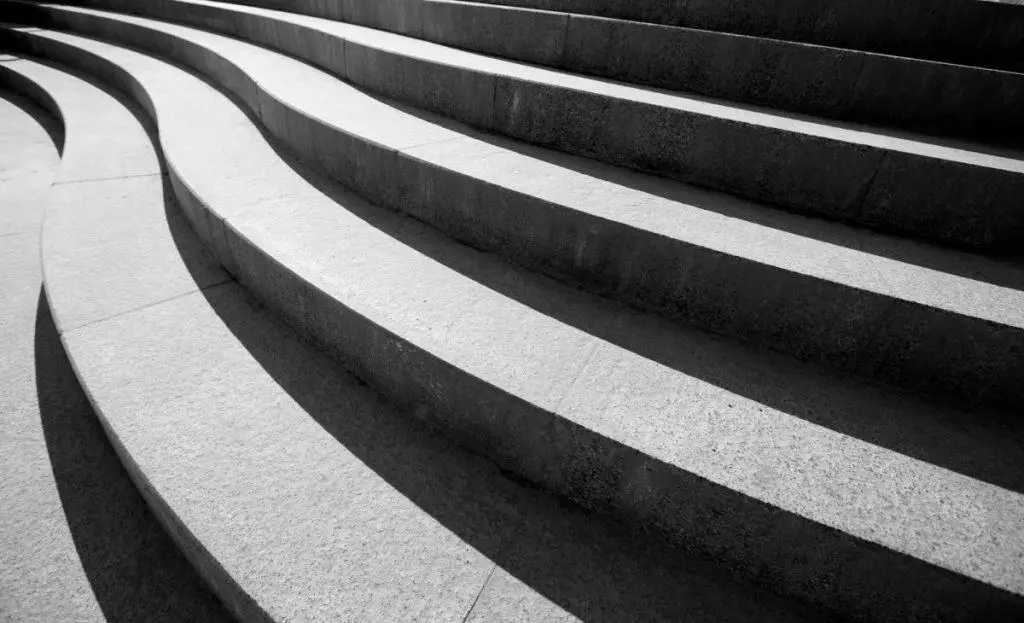
The concrete is then washed, set, and cured. Before it is fully cured, concrete can be etched, stamped, or engraved to add personalization.
Once the concrete is cured, forms can be removed, and, if you so desire, the concrete can be stained in a multitude of colors.
Overall, the installation process is pretty straight forward, but it does vary depending on what you are building. This is obvious, as you do not build a house the same way you build a road, but this is not what we are getting into. Instead, we are going to talk about the many uses of concrete.
Concrete is one of the most versatile stone-like building materials. Concrete is commonly used for sidewalks and roads, but it is also used for houses and commercial buildings, foundations, sculptures, outdoor features like benches, fountains, or gazebos, and pools.
Concrete Qualities
Concrete is a pretty astounding material to work with, especially once you realize all it is used for. Seeing all of its uses, you may be wondering why it is so popular.
The reason for concretes popularity can be chalked up to a few things: it’s extremely versatile, it’s customizable, it’s durable, and it’s cost-effective.
Read more: The Advantages and Disadvantages of Using Concrete
As we went over in the previous section, concrete can be used for almost anything. Much in the same way, it can be personalized in endless forms.
You can get your concrete colored, shaped, drawn on, stamped, polished, and painted- there is no end to the personalization it provides.
This quality alone creates a large market for concrete both commercially and residentially.
Another great quality concrete has is durability. Domestically installed concrete is usually a strength of about 3,000 PSI (Pounds per Square Inch), which is great for foot traffic, cars, and kids. This being said, concretes compressive strength can be up to 12,000 PSI.
Lastly, people love the price of concrete. Something this customizable and unique could cost an arm and a leg, but it doesn’t! Plain poured concrete is about $6.00 per square foot, meaning it won’t break the bank.
Read more: Concrete Pricing Guide: All the Facts and Figures
Tarmac
We’ve learned a bit about concrete and I hope that was fun, but it’s time to look at the next material: tarmac.
Tarmac is something we are all familiar with, even if we don’t realize it. Tarmac, short for Tarmacadam, was one of the most common road surfacing materials, if not the most common.
Sadly, many famously Tarmac surfaces (such as airport runways) are now being replaced by its close cousin: Asphalt.
Do not fret too much; Tarmac is still in use, especially for commercial projects like driveways, so it is still very eligible to be on this list of comparisons.
What Is Tarmac Made Of?
Tarmac is made up of aggregates such as Portland cement, sand, gravel, and even concrete, all mixed with tar to create a dense but flexible material.
These aggregates are mixed in and combined with hot tar to create this unique material.
Installation And Use
Tarmac is not as widely used as concrete because it is much harder to mold hot tar into the shape of a building than it is to pour concrete that way.
However, Tarmac is still a versatile and useful material. It is commonly used on roads and playgrounds, but it can also be used for roofing.
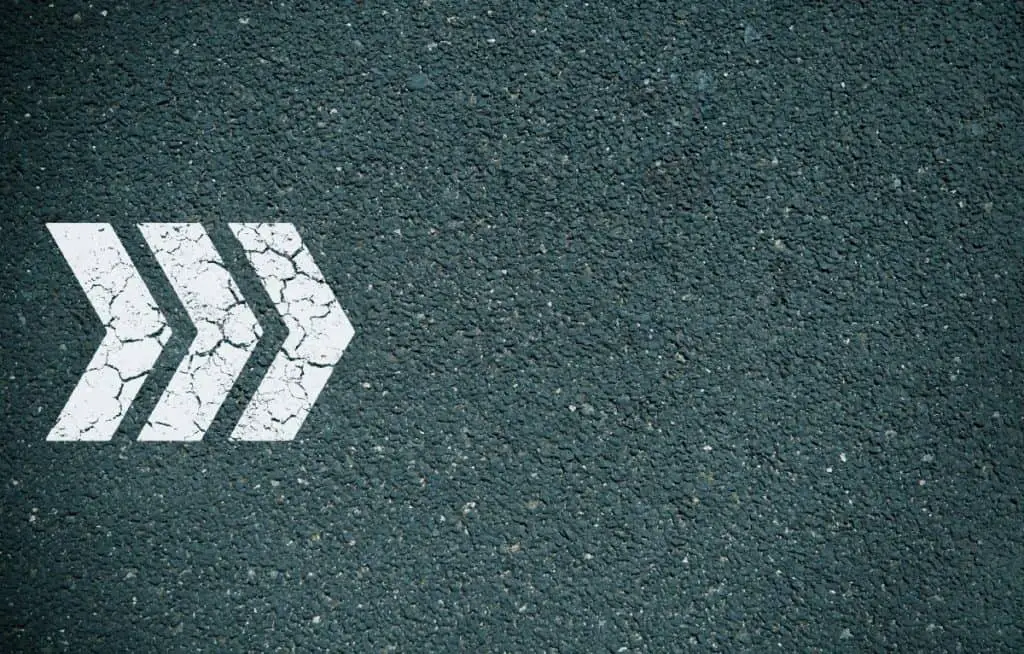
To install tarmac, construction workers must first mix the hot tar with the aggregates and prepare a place for the installation. Once these steps are done, the mixture is laid out with a vibrating roller to ensure a smooth, even application.
After the pouring, it is set, finished, and ready for use.
Unlike concrete, Tarmac is not all too customizable. It can not be etched, stamped, or stained with color, but it can be painted over. We often see this in roadways that have lane division lines, fog lines, and directional arrows.
Qualities Of Tarmac
Much like concrete, Tarmac has some unique qualities that add to people’s reasoning for choosing to use it both commercially and residentially.
Tarmac is a durable material that can withstand any weather condition. It is flexible, breathable, and can absorb water when needed.
Tarmac is also an extremely cheap material, costing a mere $1.00 through $5.00 per square foot, including labor costs.
Sadly, due to the lack of Tarmac being used in the United States, there is no accurate measurement for the minimum and maximum PSI it can handle.
Asphalt
The last material we will be taking a close look at is asphalt. 70% of all asphalt produced is used for road construction, but it does have other uses.
It has recently risen in popularity, landing above Tarmac, its dark aggregate-filled cousin, due to its intense waterproofing ability.
What Is Asphalt?
Asphalt is a building material made up of a slew of complex materials. Unlike concrete and Tarmac -both of which use mostly natural materials with aggregate bases- asphalt is made up of a component called bitumen.
Bitumen is a semi-solid form of petroleum, obtained as a residue from the process of distilling petroleum or natural deposits. With Bitumen as its base, dark aggregates are added into the mix.
A typical base-to-aggregate ratio used for asphalt is 5% bitumen and 95% aggregate. There are usually 3 aggregates in asphalt: crushed rock, natural sand, and man-made sand that is the byproduct of crushed rocks.
This mixture of aggregates is mixed into bitumen and heated to approximately 300º, combining into one solid named asphalt.
Installation And Use Of Asphalt
Asphalt is installed much like the other two types of building material, starting with the removal of old materials and the excavation of a new spot.
Once your area is excavated, you have to compact the soil to make a strong base, then, you add crushed rock over the base soil.
This base rock is essential to proper drainage wherever your asphalt may be. Rocks used under asphalt should be coarse and rough. Depending on whether your underlying soil is clay-based or sandy, you’ll need more or less crushed rock.
For clay-based soils, you’ll need about 8 inches of crushed rock as a base. For sandy soil, you need just 4 inches of crushed rock for your base.
You have to pack this rock into the base soil and let it sit for about a week before you pour your asphalt. This will allow the rocks ample time to naturally settle into the soil below.
After this week is up, you can pour your asphalt. As I said previously, asphalt is a mix of aggregate and bitumen. At this stage you choose whether you would like smaller or larger aggregate; small aggregate is often used for residential purposes like driveways or outdoor basketball courts since it gives a smoother appearance.
This fine aggregate is weaker than larger, more obvious aggregates, so if strength is your first priority, choose larger aggregates.
Once the asphalt is poured, it is compacted with a heavy roller and then treated for finishing.
One downside to asphalt is the amount of time it takes to fully cure: 6-12 months. Due to the oil base that bitumen is, asphalt takes a lot longer to completely set than either concrete or tarmac, but it also lasts longer.
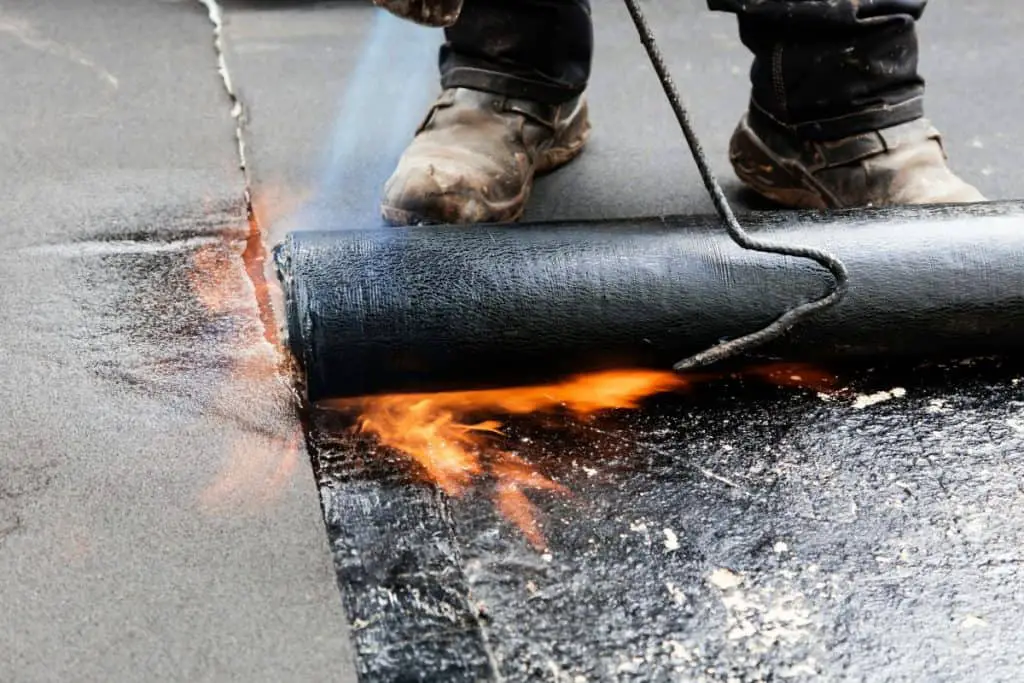
This asphalt installation and drying process is seen by many during driveway and road construction -the two main uses of asphalt-, but not as often in other areas. One way asphalt is used that is not for roads was briefly touched on earlier: waterproofing.
Bitumen (the base component in asphalt) is a petroleum derivative, meaning that it is oil-based. This makes asphalt a great waterproofing material. It is often used to line roofs, corners, and buildings before the finishing touches are put on to protect the interior of the structure from being damaged by sneaking streams of water.
Asphalt Qualities
The qualities of asphalt are somewhat of an upgraded version of the qualities that Tarmac boasts; this is a large reason that asphalt has replaced tarmac in both personal and commercial use in the modern-day.
We already went over how asphalt can be used as a waterproofing material, so no need to rehash that, but it does have other interesting qualities.
Asphalt is unmatched in the smoothness of its surface as well as its blend-ability. Unlike other surfaces, asphalt is able to be melted into itself as it is oil-based.
This means that repairs look best on asphalt. If a crack, hole, or gash appears, new asphalt can be added into that area and melted into the old asphalt, creating a seamless repair.
Asphalt is also skid-resistant, making it especially useful for roadway creation.
Some other unique qualities of asphalt are:
- Noise Reduction- Asphalt highways and roadways produce up to 7 decibels less than other roadways
- Smoothness- Asphalt is smoother than any other type of pavement, making it safe to drive on, easy on vehicles over time, and cheaper to repair.
- “Environmentally Friendly”- Asphalt is 100% recyclable and is the most recycled material in America. (By the way, did you know that concrete can be recycled as well?)
- Durability- Overall, asphalt is the most durable paving material. It is strong, flexible, and repairs can make it last indefinitely. It also has a PSI range of 3,000 to 20,000, making the max PSI 8,000 more than concrete’s.
Last but not least, the price. Asphalt, much like Tarmac, is extremely cheap, coming to just between $2.50 and $4.00 per square foot.
Related article: Asphalt vs. Concrete: Which Is Better for a Driveway?
Cross Comparison
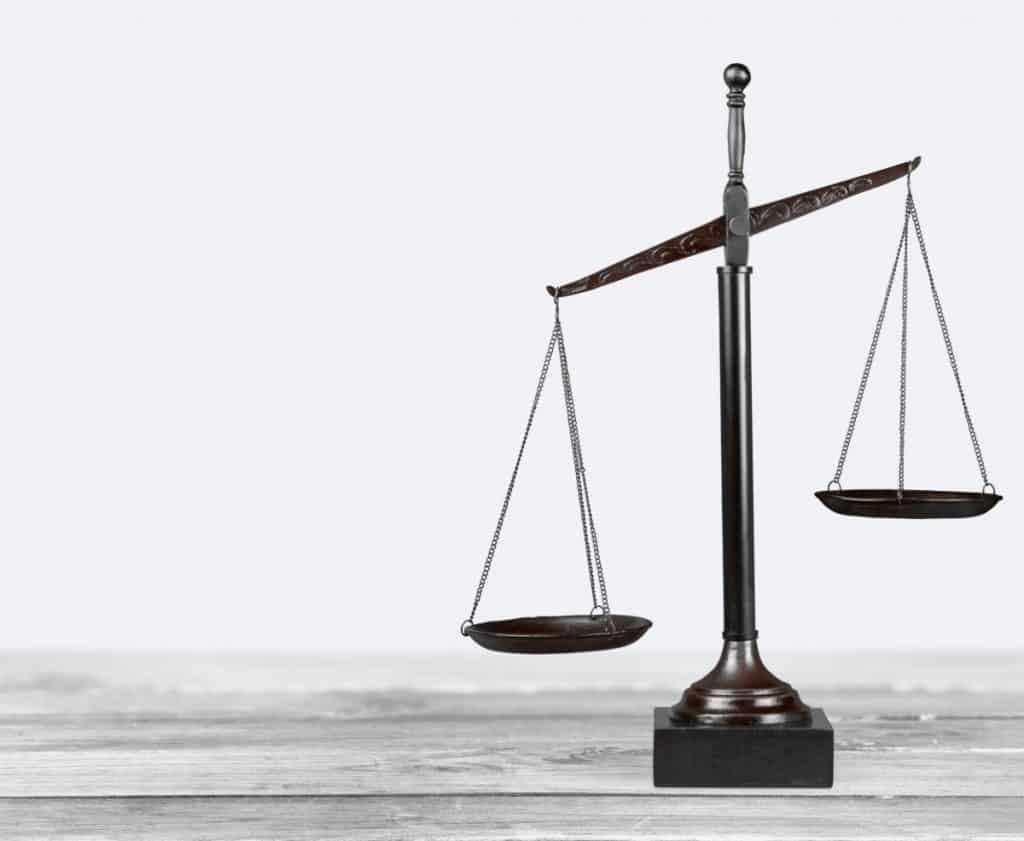
The information provided in the last three sections was thorough as can be, providing you with the differences you were wondering about when it comes to concrete, tarmac, and asphalt.
Thorough information is extremely useful, but it can be overwhelming at times. If you’re finding that all that information was a lot to take in, this is for you!
This chart lays out the differences between concrete, tarmac, and asphalt that were discussed in this article.
Factors | Concrete | Tarmac | Asphalt |
---|---|---|---|
Components | Portland cement, water, fine aggregates, and coarse aggregates. | Tar, random aggregates such as Portland cement, sand, crushed rock, and even recycled concrete. | Bitumen (petroleum derivative), manmade sand aggregate, crushed rocks, natural sand. |
Installation | -Wet installation on an excavated area. -Forms used to keep concrete in place. -Takes days or weeks to dry completely. | -Hot installation on flat surfaces. – Takes 2-3 days to cure completely. | -Hot installation on aggregate material. -Compressed and left to dry. -Takes 6-12 months to completely dry; before then it is delicate. |
Uses | -Roads -Driveways -Patios -Buildings -Foundations -Almost anything | -Roads -Driveways | -Roads -Driveways -Waterproofing |
Durability (Pounds per Square Inch/PSI) | 3,000-12,000 PSI | PSI Range N/A | 3,000-20,000 PSI |
Unique Qualities | -100% customizable -Can be used for upright and in-ground structures | -Flexible -Absorbs water | -Waterproof -Noise reducing -Smooth |
Price Per Square Foot (PSF) | $6.00 PSF | $3.00 PSF ($1.00-$5.00 PSF) | $3.25 PSF ($2.50-$4.00 PSF) |