Concrete is arguably the most commonly used material in construction. Besides its affordability and durability, concrete is a preferred construction material due to its low maintenance. And since gunite is a form of concrete, it might be difficult for some to differentiate between the two.
The main difference between concrete and gunite is through application since gunite is sprayed onto surfaces in a dry mixed form while concrete is applied directly without the use of a gun. Moreover, gunite contains extra-fine particles, unlike concrete’s balance of both small and large particles.
Curious to learn more about the differences between these two popular construction materials? Then you couldn’t be in a better place. Read on as we break down the pros, cons, and uses of both gunite and concrete.
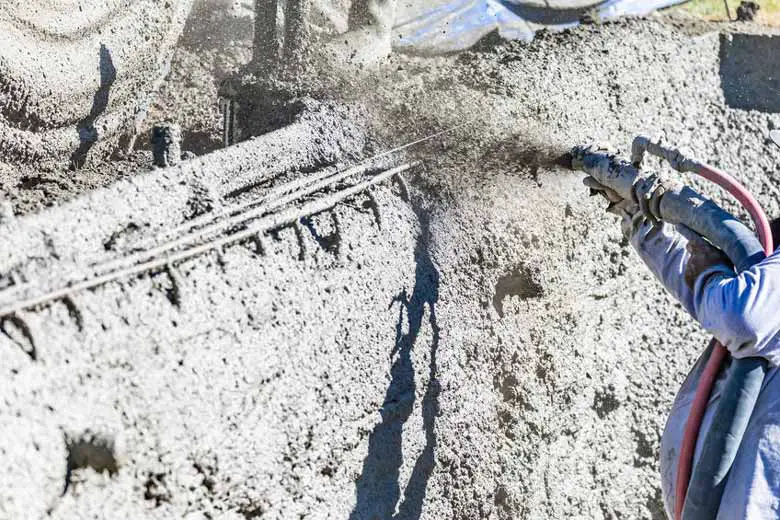
Table of Contents
What Is Concrete?
In building construction, concrete is commonly used for constructing columns, foundations, slabs, and beams, among other load-bearing structures. Concrete typically comprises cement, coarse aggregates, and fine aggregates (sand), which are mixed with water to form a binding matrix that hardens over time.
Depending on the nature of construction, concrete can also use other binding material besides cement. For instance, bitumen is used to make asphalt concrete for use in road construction, while lime can also be used to make lime concrete.
Concrete production entails the mixing of aggregate, cement, water, and other additives in calculated portions to create quality concrete. As a time-sensitive type of production, workers need to put concrete in place before it starts to harden.
Modern concrete is often prepared as a viscous fluid that can be poured into various forms, often called concrete forms. However, the challenge when dealing with concrete is ensuring the ingredients are properly mixed, shaped, placed, and handled.
Interruptions in the pouring process can lead to undesirable outcomes as the initially poured concrete can set before other layers are added.
Advantages of Concrete
- Concrete is durable. Concrete is among the most durable materials used in construction. Concrete’s longevity and resilience are attributed to its rust, burn, rot and weather-resistance, making it a genuinely long-lasting product to use in different types of construction.
- Concrete is low maintenance and recyclable. In addition to being durable, concrete is also low maintenance, explaining why it’s commonly used in commercial and home construction projects. And in case property owners opt to demolish their structures, the concrete used can be recycled and put to use in other projects.
- Concrete is versatile. Although ultra-strong when hardened, concrete can be molded into any form, texture, or shape preferred by designers (when fresh). Recent developments in the concrete industry, such as pervious concrete, photocatalytic concrete, and high-performance concrete, have increased the usability of concrete in different environments.
- Concrete is energy-efficient. Concrete can help moderate temperature conditions in a building’s interior due to its ability to store energy. This feature has several benefits, top of the list being reduced cooling and heating demand over a building’s service life. Therefore, when concrete is used in combination with technologies like hydronic heating (and cooling) systems and radiant floors, property owners can avoid a large amount of energy-related costs.
- Concrete is an emission-free material. Unlike other construction materials that can emit toxic compounds and harmful gases over time, concrete is a completely inert substance once cured. This property makes concrete a safe building material that’s guaranteed to adhere to relevant construction laws and consumer safety regulations.
Read more: The Advantages and Disadvantages of Using Concrete
What Is Gunite?
Commonly referred to as sprayed concrete, gunite is a type of concrete or mortar that is conveyed and pneumatically projected at fast speeds through a hose.
Gunite is usually reinforced by conventional steel mesh, fibers, or steel rods.
And although gunite is commonly referred to as shotcrete, these two terms have different meanings. Gunite is the dry gunned version of shotcrete, while shotcrete is the wet version of gunite.
With gunite, water is added to the mixture of sand and cement as it exits the nozzle. This means the mixture remains dry until it passes the nozzle.
As a result, the gun operator must be well-skilled in handling the cement gun to ensure the dry mixture and water mix in the recommended ratios.
Shotcrete, on the other hand, has water, cement, and aggregates mixed in the right ratios before being placed in the cement gun. Therefore, the main difference between shotcrete and concrete is when water is added.
Advantages of Gunite
- Gunite becomes harder once it cures. Since gunite is only mixed with water at the point of exiting the hose’s nozzle, it has great potential of making extra hard bonds after curing. This enhances the durability of pools, domes, or tunnels that use gunite as part of their primary construction.
- Gunite has a high compressive strength. Although gunite is still a type of concrete, it stands out from normal concrete due to its impressive compressive strength. Structures made from gunite can achieve compressive strengths within the range of 7,000-9500 psi, making them both durable and ultra-strong.
- Gunite doesn’t have time limitations. Unlike other types of concrete that must be placed before the mixture hardens, gunite allows for start and stop construction without the risk of shrinkage cracks. Construction workers can start and stop with the project without the need to create a plane of weakness or cold joint. This is because the high velocity of gunite application allows for the formation of tough bonds.
- Gunite allows for unique constructions. Guniting is a great strategy when dealing with unique structures such as swimming pools, tunnels, domes, and ditches. While normal concrete can still work on such structures, gunite provides a better way to make strong bonds as the high-velocity impact ensures the new structures have the required compressive strength to withstand different types of load-related pressure.
- Gunite is durable. Most swimming pools use gunite and concrete due to the high velocities associated with their release. Gunite, once applied correctly, can last for several years without the need for modification or maintenance. However, for the gunite to have the desired strength, the guniting process must be conducted by skilled experts that understand how to mix water and gunite in the required ratios.
Differences In Production
Concrete relies heavily on a mixture of fine and coarse aggregates. Some of the commonly used aggregates in concrete production include crushed stone, natural gravel, and sand. Recycled aggregates are also becoming increasingly popular alternatives to natural aggregates.
Concrete production can either be large-scale or small scale, depending on the type of project. For large-scale purposes, concrete production occurs in a concrete batch plant. There are two main types, central mix plants and ready-mix plants.
Central mix plants are best for accurate control as they tend to mix all concrete components, including water. On the other hand, ready-mix plants don’t add water to the mixture of cement and other aggregates.
Gunite uses a dry mix of concrete. It is usually pre-mixed in the preferred ratios before being loaded into a hopper.
It’s important to note that, on most occasions, gunite doesn’t incorporate coarse aggregates in its production.
Small aggregates are preferred when spraying concrete to reduce the chances of rebounding when applied on a surface at high velocity.
Unlike concrete which may or may not include a mixture of water before being delivered on-site, gunite only uses a dry mix. If water is added to the mixture, then the gunite becomes shotcrete.
Use in Construction
Concrete is a highly versatile construction material with tonnes of applications. But before concrete is used in construction, it’s important to determine the appropriate concrete type. It is commonly used in building and road construction due to its toughness and malleability.
Some of the common applications of concrete include building materials, more specifically commercial buildings and homes. Concrete buildings often require little maintenance and tend to last long.
Related Article: Buying a Concrete House: a worthwhile investment?
This is mostly due to concrete’s resistance to wind, fire, and even hurricanes. Moreover, concrete is also used in roads and highways due to its ability to withstand pressure from heavily loaded vehicles.
Concrete is also a useful material when constructing bridges, more specifically bridge superstructures. You’ll also find concrete being used in the construction of sidewalks, decks, curbs, and barrier walls.
Generally, concrete can be used in any type of construction provided the right type of concrete is used.
Although not as versatile as concrete, gunite is a useful material for specific applications. Gunite makes a great material when used for retention walls and slope stabilization. The sprayed concrete usually works well once a framework is in place.
Besides dikes, dams, and ditches, gunite is also preferred when constructing concrete swimming pools.
The ability of sprayed concrete to provide the required reinforcement (due to high-pressure levels) also makes gunite an ideal material when building tunnels.
Gunite is also commonly used in dome construction. Most construction workers love the ease of concrete application that comes with both shotcrete and gunite. The challenge with gunite, however, is the need to adjust the water ratio regularly.
Application
Concrete is applied to construction projects through pouring. The specific type of placement depends on the nature of the construction. For large construction projects, the concrete usually comes in a truck (ready mix), which usually has a spinning drum to prevent the concrete from settling.
Once the concrete is released from the drums, it is poured into the forms while wet. This is the main difference between concrete and gunite.
Concrete is poured gradually and carefully into forms without any form of pressure. Construction workers usually use rakes and shovels to prevent the formation of air pockets once the concrete is being poured.
Gunite application is different from how normal concrete is applied.
Instead of being poured on a preferred form, gunite is usually sprayed or shot from a cement gun, hence the term `gun-ite`.
Before construction, builders usually load a dry mix of cement and soft aggregate into the preferred delivery equipment.
Compressed air is then used to send the mixture to the nozzle, where it mixes with water as it’s being shot. Shotcrete, although different from gunite, is also applied the same way through spraying.
The compressed air ensures gunite lands on the target surface with great impact, which in turn allows for a strong, compact bond. On most occasions, gunite is usually sprayed or shot on a rebar framework, which allows for increased versatility in terms of design.
The Different Types of Gunite and Concrete
Concrete comes in many types and styles to suit building and construction needs. The most common type, however, is ordinary concrete which includes a mixture of water, sand, cement, and coarse aggregates.
High-performance concrete is also another concrete type that is specifically designed to have higher strength, durability, and workability than ordinary concrete.
Reinforced concrete is also another concrete type that uses various steel forms as reinforcement. Combining steel (high tensile strength) and concrete (high compressive strength) gives reinforced concrete unique strength and durability properties.
Another popular type of concrete is precast concrete, which entails casting concrete into forms or mold in controlled environments. The resulting concrete is then transported to the site once it has hardened.
In precast concrete, the concrete is cured in controlled environments where humidity and temperature are closely monitored.
Pervious and lightweight concrete are also other concrete types commonly used in construction. Concrete is considered lightweight if it has a density of less than 240 kg/m3.
This concrete type improves fire resistance and a structure’s thermal abilities. Pervious concrete, on the other hand, allows water and air to circulate through a series of voids and holes.
Gunite doesn’t have as many alternatives as concrete in its primary form. And as mentioned earlier, gunite obtains its name from the cement gun that shoots the concrete at high pressure.
However, sprayed concrete can be of two main types, either gunite or shotcrete.
Again, as revealed in the early sections, shotcrete is similar to gunite as it’s shot from a nozzle in high pressure such that it forms a compacting matrix on the target surface.
The main difference between shotcrete and gunite is that shotcrete isn’t loaded on the gun dry. It comes in a wet cement truck before being loaded and short out of a nozzle.
Shotcrete takes less time to apply compared to gunite. Moreover, shotcrete doesn’t rebound off the surface, meaning you reduce the probability of weak spots when using the technique.
Some disadvantages of shotcrete include the formation of shrinkage cracks (if not well applied), costlier than gunite, and cannot be used in start-stop construction.
Compressive Strength
Concrete, when poured, has a fairly good compressive strength. You’ll find that many concrete mixtures can be modified to have stronger durability and mechanical properties, which helps enhance a building’s structural integrity.
The average compressive strength of residential concrete stands at 2500 psi, while residential concrete can have a compressive strength of 4,000 psi. However, certain applications can have incredible compressive strengths surpassing the 10,000 psi mark.
Gunite is ideal for use in swimming pools and tunnels due to several benefits, top of the list being its ability to become extra hard upon curing.
It has a compressive strength ranging from 7,000 -9500 psi, making it ideal for use in applications with high compressive loads. However, for the gunite to hold its weight and have desired outcomes, experienced, well-skilled nozzlemen will be needed.
Construction Process
Concrete has a fairly straightforward construction process. However, the steps of concrete construction depend mostly on the type of structure or building you’re working on. Precast concrete is usually transferred to the construction site, while cast-in-site concrete will need construction workers to mix the components in the right amount.
Once the concrete is poured into the mold or formwork, it is then vibrated or expertly shoveled to allow for proper compaction. The formworks are then removed before being used as desired in the construction project.
Similarly, the steps in applying gunite in construction depend on the type of construction. But for general gunite constructions, experts will first need to set up a solid rebar structure. Reinforced structural steel helps to prevent the gunite shell from any defects or cracks.
The rebar framework mostly consists of horizontal and vertical bars that enhance the structure’s overall strength. Once the rebar framework has been carefully installed, contractors then load the dry concrete before it’s shot onto the rebar through a high-pressure nozzle.
Another nozzle simultaneously releases water that mixes with the gunite immediately; it exits the gun’s high-pressure hose. The gunite shell is then allowed to cure for several days before further construction can proceed.
Wrapping It Up
Although concrete and gunite have a lot of similarities, they do come with their own differences, thus explaining why the two terms cannot be used interchangeably.
While gunite can be referred to as a type of concrete, its application is completely different from normal concrete. This is because gunite is shot from a hose in high velocities, thus making strong bonds on the target surface.
On the other hand, concrete is mostly poured into forms, which allows builders to come up with different shapes and sizes of concrete.